
Warehouse Management
IE Business SchoolMasters in ManagementOperations Management - Prof. Felipe QuintanaSection 3Vishal Darak‘A warehouse is a planned space for the storage and handling of goods and material.’In general, warehouses are focal points for product and information flow between sources of supply and beneficiaries. However, in humanitarian supply chains, warehouses vary greatly in terms of their role and their characteristics.The motivation behind me choosing this topic was my idea. I am currently working on open warehouse system for the retail stores. So by choosing this topic I gained many insights on warehouses. The complexity involved in opening a warehouse and operating it.

Global Warehouses
The global warehousing concept has gained popularity over the last decade as stock pre-positioning becomes one of the strategies for ensuring a timely response to emergencies. They are usually purpose built or purpose designed facilities operated by permanent staff that has been trained in all the skills necessary to run an efficient facility or utilising third party logistics (3PL) staff and facilities. For such operations, organisations use, information systems that are computer based, with sophisticated software to help in the planning and management of the warehouse. The operating situation is relatively stable and management attention is focused on the efficient and cost effective running of the warehouse operation. Numerous organizations have centralized pre-positioning units strategically located globally. Some of these offer extended services to other humanitarian organizations on a cost plus operating charges basis.
Local Warehouses
Field Warehouses are usually temporary in nature. They may be housed in a buildings which was not designed to be used as a warehouse, in a temporary building/structures, and are often in mobile units (rub halls, Wiikhalls) that are little more than a tent in a field. The initial staff may be a casual workforce that has never worked in a warehouse before and the inventory system is more likely to be paper based. Often the situation is initially chaotic, sometimes dangerous and coupled with a humanitarian need which may be very urgent. The management style must therefore be practical and action oriented with a focus on making the humanitarian goods available as quickly and efficiently as possible, while being accountable at the same time.
P&P
Policies
The policies contain hard and fast rules and regulations that define the general conduct of the warehouse operation. Examples of the types of policies that organisations will define are as follows:organisational specific health and safetyhuman resources managementsecuritypest controlwarehouse maintenance and cleaningquality controlrecord keeping and reportingreverse logistics – Return of goods and exit strategy in the event of downscaling or shutting down operationsdisposal of obsolete and damaged goods.
Procedures
The procedures' document defines step by step how the activities in the warehouse should be carried out and clearly defines the processes to be adopted. These can be adopted as ‘best practice’.The procedures provide visibility of the operations for managers and donors.However, in creating such procedures, care must be taken to avoid constraining the use of local initiative which might be required to deal with local conditions. Procedures should be considered as streamlining the business processes and providing checks and balances. They provide guidance to warehouse managers and must have some level of flexibility to cater to unique situations. This can be achieved by limiting the level of detail that the procedures document defines, allowing more flexibility and/or by arranging ‘dispensations’ to allow departure from the procedures in order to optimise local performance, especially in emergencies.The procedures will normally provide the step by step guidance on how to manage each aspect of warehousing and may cover:receiving and issuing of supplies;quality control or verification;storage of goods;how to control stock movement (stock control);documentation flow;how to detect and deal with stock losses;how rejected material will be managed; andhow to deal with unwanted material, obsolete and scrap, disposal.
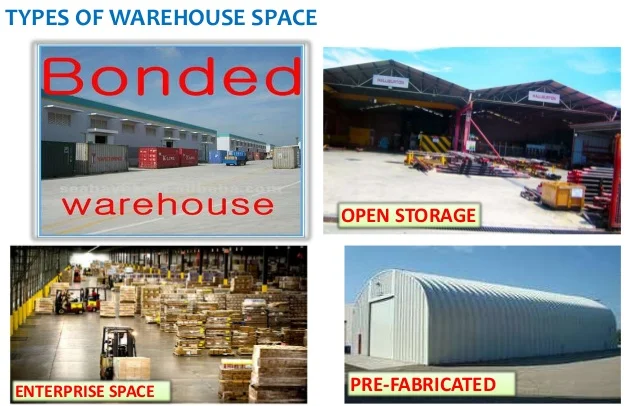
Types of Warehouses
Commercial
in rented building used for business.
Government or State
such as at the ports or harbours. This is common in emergency situations.
Transit
for temporary storage of goods destined for different locations and need storage for a very short time.
Bonded
for storage of goods whose duty is unpaid and especially where the goods are destined to another country. Pre-positioned stock is often held in bonded warehouses so that export is quick and can sometimes be stored for long periods.
Open Storage
not ideal for perishable products but in emergencies, sometimes the only alternative.
Organization
Space that is owned and managed by the organisation.
Pre fabricated
Pre-fabricated warehouses where there are no permanent structures available. This is common practice in emergencies.
Principles of Warehouse
Planning Inbound receipt Procedures
Storage Formalities
location managementinventory controloccupational health and safety
Outbound Delivery Procedures
Setting Up Warehouses
Determining NeedsIn determining needs, one should look beyond the basic need of a warehouse to store things. Whilst, this is correct there are also other considerations.the volume of goods;speed of through-put required;as a transit point;breaking bulk location;an area for sorting and consolidating different goods;to enhance the speed of the response;to protect and account for inventor; andas a buffer in the event of a break-down or delay in the supply pipeline.
Toyota Warehouse Setup
Determining Storage Requirements
Suitable Location
There are a range of factors to consider when deciding on the location of a new warehouse facility and these may vary depending on whether you are selecting a location for a temporary building or selecting from one of a number of existing buildings.These may include:proximity to ports of entry and beneficiariesexisting buildingssecuritythe contextsite conditionaccessservicesland size availablepurpose of warehouseprevious use of the facilityfloor weightaccess to labour
WareHouse Selection
Factors to consider:nature and characteristics of goods to be stored;nature of handling equipment available;duration of storage needed i.e. short term or long term;the need for other activities, e.g. repackaging, labelling, kitting, etc;access and parking for vehicles;number of loading docks required; andsecure compound.
WareHouse Preparation Planning
Space Layout
The areas that should be planned are both the general storage areas and the areas for goods receipt, consignment picking and goods dispatch. It is also desirable that space should be set aside for the following activities:equipment maintenance and parking;charging of equipment batteries such as pallet trucks;refuelling of trucks;an area for garbage disposal e.g. empty packaging;a quarantine area for keeping rejected goods, goods to be sent back or destroyed;an employee rest area;washroom; andan administration office.
Planning
It is worth keeping these requirements in mind during the planning of the main operating areas. Planning consideration needs to be given to the following:allocate space for each type of product and locating number;allow sufficient space for easy access to the stacks for inspecting, loading and unloading. Stacks should be one meter from the walls and another meter between stacks;sizing the goods receipt and despatch area;allow space for storage of cleaning materials and supplies;allocate areas for damaged items by consignment number;allow sufficient space to repackage damaged items and place it in separate stacks;sufficient free space is needed to operate a warehouse effectively. When planning the size of a warehouse consider:planning on having about 70-80% utilisation of available space, whilst considering:throughput ratenumber of stock keeping units (SKU)handling characteristics of items, etc.
Special Storage Needs
Some relief items require special attention in terms of the type and security of the storage area. For example:Medical supplies and drug shipments can contain a large number of small, highly-valued and, often, restricted items, many with a limited shelf-life. Thus, a secure area is required, as well as judicious attention to expiry dates.Hazardous products such as fuels, compressed gases, insecticides, alcohol, ether and other flammable, toxic or corrosive substances must be stored separately, preferably in a cool, secure shed in the compound but outside the main warehouse.Antibiotics and vaccines may require temperature-controlled cold storage arrangements, with sufficient capacity and a reliable, as well as a back-up, power source.With combustible items, such as alcohol and ether, specific attention is required when storing and handling. need to be implemented to prevent wasteful surpluses and to ensure proper stock rotation. to avoid costly losses due to expired goods. Procedures for controlling, preserving and releasing medical supplies and drugs should be established in consultation with the medical experts.
Space Utilisation and Handling
the warehouse operation is composed of four key work activities:goods receiptstoragepickinggoods dispatchTo estimate the resource requirement for the whole warehouse, one should start by estimating the requirements for each of the key work activities in turn and the level of demand. Then, the resource requirements for all activities should be combined together, taking into account the way that the activities are phased during the working day, in order to make an estimate of the total resources required.
Managing Inventory Levels
It has been established that the role of inventory management is to ensure that stock is available to meet the needs of the beneficiaries as and when required.Inventory represents a large cost to the humanitarian supply chain. This is made up of the cost of the inventory itself, plus the cost of transporting the goods, cost of managing the goods (labor, fumigation, repackaging, etc) and keeping the goods in warehouses. The inventory manager's job is to make inventory available at the lowest possible cost.In order to achieve this, the inventory manager must ensure a balance between supply and demand by establishing minimum holding stocks to cover lead-times. To achieve this, the inventory manager must constantly liaise with the programs to keep abreast of changing needs and priorities. The warehouse must always have sufficient stocks to cover the lead-time for replacement stocks to avoid stock-outs.
Reorder Level Policy
The reorder level is the level of the stock of a particular item, held by the firm, when an order is needed to be placed for avoiding the risk of being out of stock. It is based on the average time taken by the supplier for replenishment, maximum usage of the item during the replenishment time, and safety stock requirement. It is also known as reorder point.Reorder level = (average daily usage rate x average lead time in days) + safety level
Reorder Quantity Policy
The reorder quantity is the quantity of the order that is to be placed on a new purchase order for the particular item. The ordered quantity or the number of units needs to be optimum taking into account the various factors like cost of order, cost of transportation, carrying costs, etc. The reorder quantity is the quantity which, given the normal usage, provides the best balance between the various factors like quantity discounts, freight, storage costs, and working capital requirements. Reorder quantity = SQRT(2 × quantity required × cost per order/ carrying cost per unit)
Takeaways
1. Organization is kingIf your warehouse is not organized, incoming products will not go to the appropriate locations. Pickers will spend needless hours trying to find products. You must establish a system that organizes your materials in a logical and defined order.2. Start with the right receiving When materials come into your warehouse, they should be verified and inspected immediately. Shortages or damages require immediate notation. 3. Apply logic to pick processesWhether your warehouse is small or large, the amount of time spent picking orders is a large portion of your costs. If your warehouse is organized efficiently, you can organize pick lists for better time control.4. Reorganize when neededWhat works for your warehouse today may not work six months from now. Reevaluate your inventory and storage methods periodically to make sure that you maintain the right product flow.5. Use quality controlWhen products are sent to your shipping station, the items must be verified before they are actually packed and processed. Packers do not normally have time to double-check each item. 6. Keep your warehouse safeMaintaining a safe environment is very important to maintaining peace of mind. You have to meet certain requirements, and protecting your employees from injury is a key goal. 7. Maintain appropriate lightingA brighter warehouse provides not only a safer work environment but also improves your employees’ ability to do their job. 8. Train your staff Since processes change from time to time training employees (whether seasoned or new) will always be required. Schedule time for training and retraining when needed.9. Use the right softwareYou have a vast number of choices in software for material handling and warehouse management. Programs can be used for inventory control, labor, equipment maintenance, shipping and more. 10. Ensure prompt delivery and customer service Whether you run your own transportation or use an outside carrier, use a shipment-tracking program.
Future Warehouses
Alibaba
SAP
Amazon
Stock Control and Movements
The warehouse/inventory manager is responsible for monitoring the movement of goods as they are transported from the supplier and for the control of stock movement in the warehouse facility.The vital stock control measurements include:establish levels of operating stocks based on consumption/rate of usage. The stock levels shall be reviewed from time to time depending on current needs. ensure that weekly and monthly stock balances reports of each stock item and the total value are prepared;maintain monthly stock usage report of each item kept in the store and the overall in the usage trend in last six months;review and report on six monthly basis slow moving items indicating the last movement date the unit value and total value and liaise with user department;establish quantity, lead -time and availability of each item supplied on the market;keep a record of all non- stock items received from suppliers, returned to suppliers and issued out to users.
Related to Our Class
5S for WareHouses
Lean WareHouses
Wastes
Customer Experience
WareHouse Management System
A warehouse management system (WMS) is a software application, designed to support and optimize warehouse or distribution center management. They facilitate management in their daily planning, organizing, staffing, directing, and controlling the utilization of available resources, to move and store materials into, within, and out of a warehouse,while supporting staff in the performance of material movement and storage in and around a warehouse.
Planning
finalizing the daily plan for receiving dock activity, selecting the workload/orders to be processed in the day or shift, (this may also be done by the business system), and calculating an estimate of the labor and vehicles required to pick and ship the orders to ensure the staffing is appropriate, and carriers are notified in time to meet the daily requirements.
Organizing
sequencing the orders to be picked. Organizing orders for picking can be accomplished in many ways, meeting the needs of the user. The primary objective is to be intentional, and not to pick the orders in the sequence in which they were received unless the company wants to pay a carrier make sense for transportation and delivery. The initial way of organizing was called Wave Planning with two objectives, a. to minimize need for dock staging space, by having orders arrive at the shipping dock in trailer load sequence, and b. to create an order of flow that will support monitoring the progress through the day and eliminate/reduce last minute requests for overtime or delay of carrier departure, etc.
Staffing
assign staff to work functions and areas, by Wave, to minimize staging.
Directing
ensuring the documented processes and procedures are embedded in the WMS and are consistently applied, used and appropriate for the nature of the work and service level intentions of the company (e.g., International Standards Organization 9000 (www.iso.org)). This function may also be used to divide individual orders into logical work units and the ability to assign them to separate individuals for performance, consistent throughput requirements and physical layout, e.g., separating individual case picking from each unit picking, and individual pallet load picking, to improve productivity and supporting Control.
aControlling
providing milestones for management to monitor progress through the day, providing the opportunity to respond to problems in a timely way, and report data for performance analysis.
Legal Considerations
Leasing Temporary Warehouses/Contracting.The common practice in emergencies is to lease or rent, not purchase warehouses. In this situation, there is often a shortage of suitable buildings or locations for warehouse space and this can often cause the costs to increase significantly. Therefore, it is often necessary to utilise temporary warehouse space for as short a time a possible.Care must be taken with the drawing up of the lease agreement with the owner. The following items are basic inclusions and in a lease agreement:the cost for the lease;the duration of the lease agreement;exit clause: the period of notice required for terminating or extending the lease period. Confirmation of the existence of property insurance, covering third-party, fire, water damage, window breakage, etc;details of any security arrangements;a detailed inventory of any equipment, fixtures and fitting included with the building and detailed description of their condition;confirmation of either sole tenancy or details of other tenants;information about the ground or floor strength per square metre;the weight capacity of any equipment such as forklifts, racks and shelves;in situations where neutrality is important, care must be taken to establish the actual owner of the building, which might be different from the ‘lessor’ of the building e.g. the military, religious groups or government;force majeure;indemnity; andinsurance.
Resource Requirements
In addition to the work methods, equipment and space requirements it is essential that the warehouse is adequately resourced. This is done by planning or estimating the requirements for people and equipment in order to operate the warehouse facility.There is a trade-off to be made between the people and handling equipment requirements for any given workload.In global warehouse operations, which are run like commercial operations, the focus is on minimising the cost of running the operation. In this situation, it is often better to invest in handling equipment and reduce the dependence on people resources.However, in field operations, many humanitarian organisations prefer to hire local labor which provides employment instead of relying on handling equipment.
Inventory Types
Inventory is defined as a stock or store of goods. These goods are maintained on hand at or near a business's location so that the firm may meet demand and fulfill its reason for existence.
Batch Size Stocks
1) Ordering Stocks2) Changeover Costs
Safety Stocks
1) Inventory Costs2) Out of Stocks Costs
Transit Inventory
Transit inventories result from the need to transport items or material from one location to another, and from the fact that there is some transportation time involved in getting from one location to another. Sometimes this is referred to as pipeline inventory. Merchandise shipped by truck or rail can sometimes take days or even weeks to go from a regional warehouse to a retail facility. Some large firms, such as automobile manufacturers, employ freight consolidators to pool their transit inventories coming from various locations into one shipping source in order to take advantage of economies of scale. Of course, this can greatly increase the transit time for these inventories, hence an increase in the size of the inventory in transit.
Anticipation Inventory
Oftentimes, firms will purchase and hold inventory that is in excess of their current need in anticipation of a possible future event. Such events may include a price increase, a seasonal increase in demand, or even an impending labor strike.
Capacity Inventory
1) Demand Fluctuations2) Set up Time
Work in Process
Work-in-process (WIP) is made up of all the materials, parts (components), assemblies, and subassemblies that are being processed or are waiting to be processed within the system. This generally includes all material—from raw material that has been released for initial processing up to material that has been completely processed and is awaiting final inspection and acceptance before inclusion in finished goods.
Strategic Stocks
Supply Chain Risk
Dead Stocks
No Demand
Warranty Stocks
Spare Parts
Insurance Inventory
Regulatory Requirements
Consignment Stocks
Supplier Owned