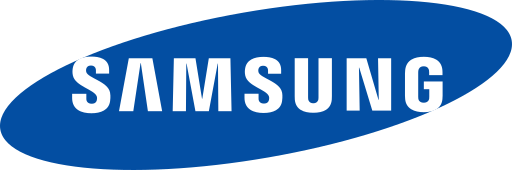
IE Business schoolMaster in Management, Section 2Operations and Supply Chain ManagementProfessor Felipe QuintanaTatiana KimSamsung Group is a South Korean multinational company located in Seoul, South Korea. It contains many different subsidiaries and affiliated businesses:Consumer ElectronicsIT & Mobile CommunicationsDevice SolutionsI have chosen this company because today Samsung Electronics has proven to be one of the most successful global brands to follow. In terms of supply chain management, they have demonstrated the operational excellence that leads them to be one of the most sustainable company. Another reason why I decided to analyze operational and supply chain aspects of Samsung is that consumer electronics have some of the most complex Supply Chain in the world. Its products incorporate hundreds of highly-engineered components, making product quality control trickier than some other consumer goods.
Operational innovation
The idea of Operational Innovation is vital for Operations and Supply Chain Management. During the session 1 we obtained the essential knowledge about it:Differerence between Operational Excellence and Operational InnovationWhy it is important for any companyRevealed OI characteristicsShowed at some examplesFor Samsung Company operational innovation is the key driver in the process. They continuously create innovations through machine vision, automated mobility, high-performance computing and connectivity.
Intelligent factory. Samsung Nexplant
In the following video you can see Samsung Nexplant - AI-based intelligent factory platform. Company is always striving to innovate all manufacturing processes.Samsung has been at the cutting edge of advanced manufacturing technologies for decades. Due to digital transformation company managed to increase its productivity and hence improve production quality.
Blockchain
Blockchain technology can accurately automate many of the current functions that require much slower and more costly human interaction.Samsung SDS, will take on 1 million shipping units and 488,000 tons of air cargo. The company believes that this technology will allow for a faster and more efficient flow of those shipments and could ultimately quicken the pace of product launches.
a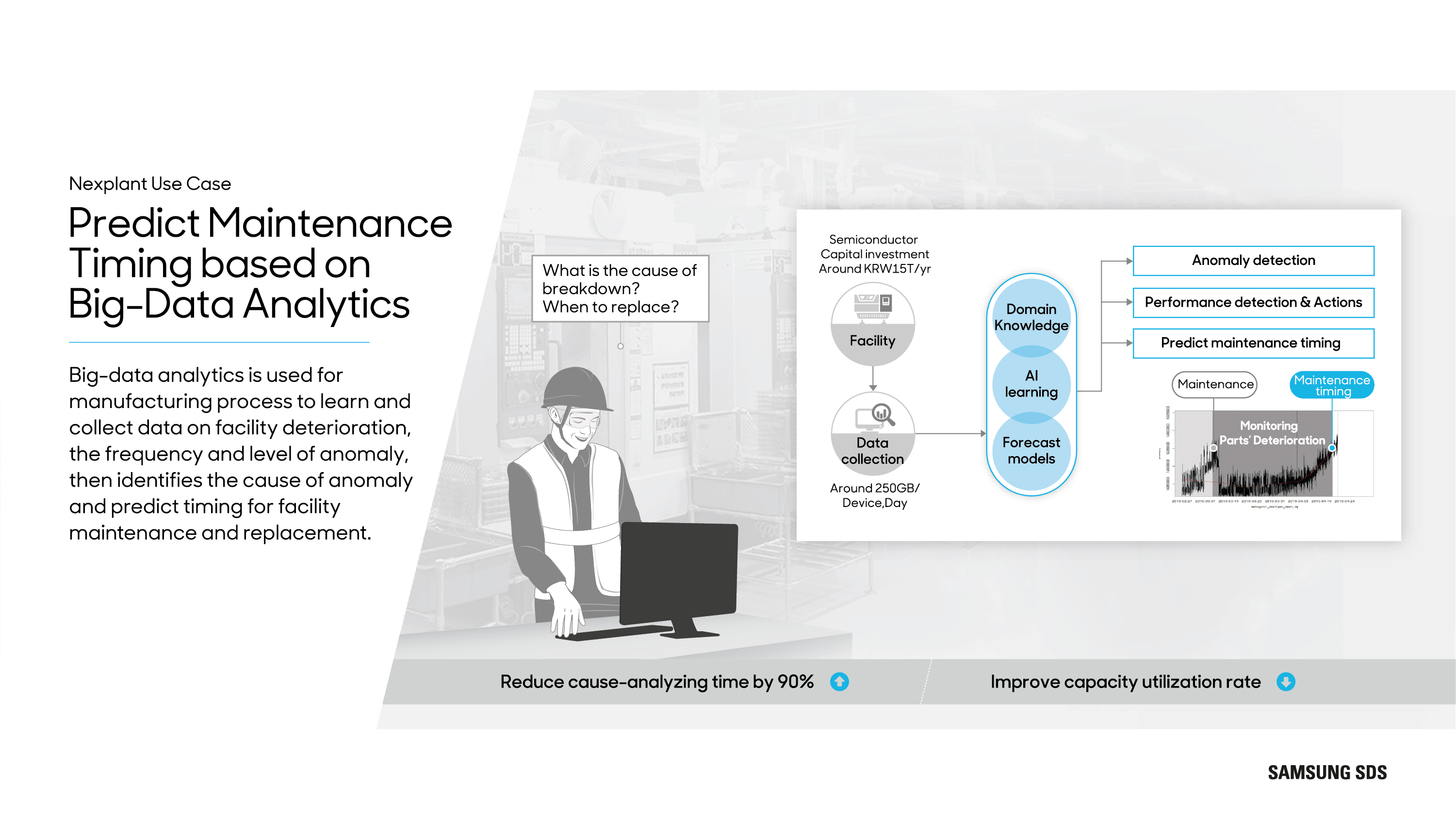
Big Data
Big Data analytics is used for manufacturing process to learn and collect data on facility deterioration, the frequency and level of anomaly , it helps to reveal causes of errors and predict timing for facility maintenance and replacement.
Samsung Cello Loading Optimizer
On the following video you can see the innovative technology called Samsung Cello Loading Optimizer that helps warehouse workers stack up boxes on a pallet or in a container in the most efficient way.
Lean Management
As we saw from the Session 7 Lean Management is the key concept in O&SCM. We discovered 25 different toolsand discussed the Toyota Production System Case.Samsung aims to deliver value to its customers and be the leader in the market. Company applied some concepts from Lean Management:6 Sigma is core and vital for the companySRMKaizenTotal Quality managementERP
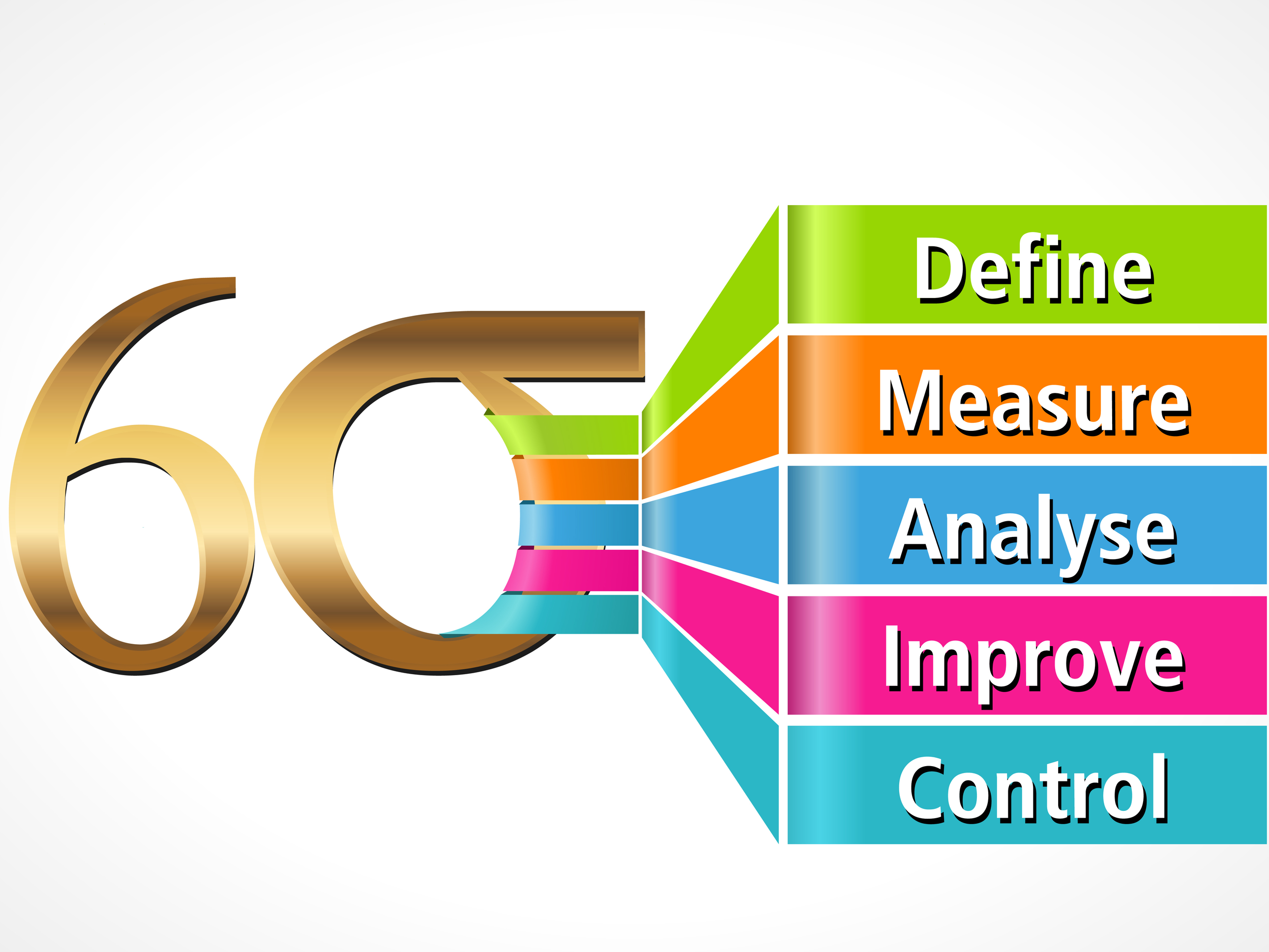
6 Sigma
In 1994, The Group decided to exploit the potential synergy linking supply chain management and Six Sigma. It created a supply chain solution with six components that play crucial roles in enhancing vendor management strategies. Due to implementation of the tool company has changed its image in world market.

SRM
Samsung evaluates potential suppliers based on the pillars that include EHS (environment, health and safety), labor and human rights, and Eco-Partner standing. Companies are required to comply with regulations regarding the handling of chemicals of concern, bans on discrimination and inhumane treatment and social and environmental impact, among others.An open-sourcing program is used to allow companies to apply to become Samsung suppliers. The International Procurement Center (IPC) and Global Supplier Relationship Management System (G-SRM) accept submissions from organizations that want to propose use of their components or materials for Samsung products.All suppliers are required to adhere with international standards under The Samsung Electronics Supplier Code of Conduct.
Kaizen
The core principle of the SCM system of the company is continuous improvement. Samsung engages in many activities to improve its performance. Most of the improvements have impacts on external stakeholders. Improvements done on Samsung phones, for example, would lead to reduction of costs and influence the supply chain management to reduce costs through different internal and external efficiency parameters.

Total Quality management
Samsung established a quality management system and apply it to all the projects that they execute. Quality Management team constantly measures and improves the quality level through preventive quality management activities and campaigns.The attached video illustrates how the company conducts drop tests for it smartphones.
Drop test
ERP
Logistics is handled in a unique way in Samsung so that it covers many administrative processes. It is more complex than described in a basic value chain model. Core building blocks for components plus combined internally and externally sourced components are shipped to the assembly factories, either from Korea or directly to the overseas plant by Samsung Electronics Logitech which handles both inbound and outbound logistics and goes further in handling payments and processes with outsourced companies working seamlessly with the global ERP system maintained by Samsung SDS.
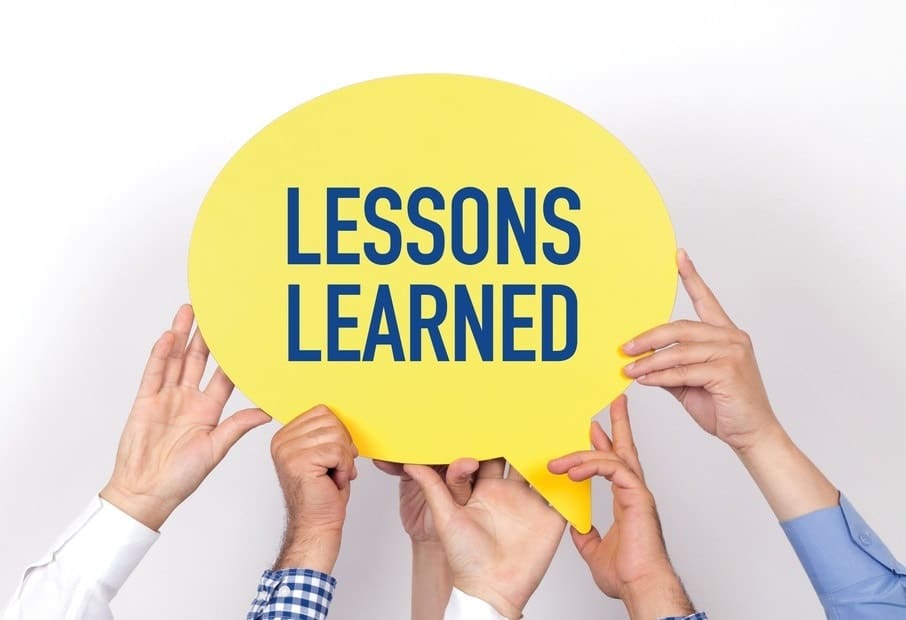
Key takeaways
Electronics industry is one of the most dynamic nowadays.There is always a big room for improvement. I believe that Samsung will continue growing as the leading electronics company in the future. It is important to mention their operations not only reduce time and cost but also help them to provide superior services.We also revealed that Samsung risk mitigation strategies are mainly to reach low inventory level, flexible capacity and redundant suppliers.In order to compete in the global market of electronics industry, company should be flexible and moreover optimize its supply chain. Although currently, Samsung does not need significant changes in operational management, I would suggest them to focuse on demand and supply risks which are imperative, also keep attention to Alignment with suppliers.

Samsung was founded by Lee Byung-chul in 1938 as a small trading company with forty employees located in Su-dong.After the Korean War Lee expanded his business into textiles and opened the largest woolen mill in Korea. Samsung first entered the electronics industry in 1969 with several electronics-focused divisions—their first products were black-and-white televisions. During the 1970s the company began to export home electronics products overseas. At that time Samsung was already a major producer in Korea. The late 1970s and early ’80s witnessed the rapid expansion of Samsung’s technology businesses.
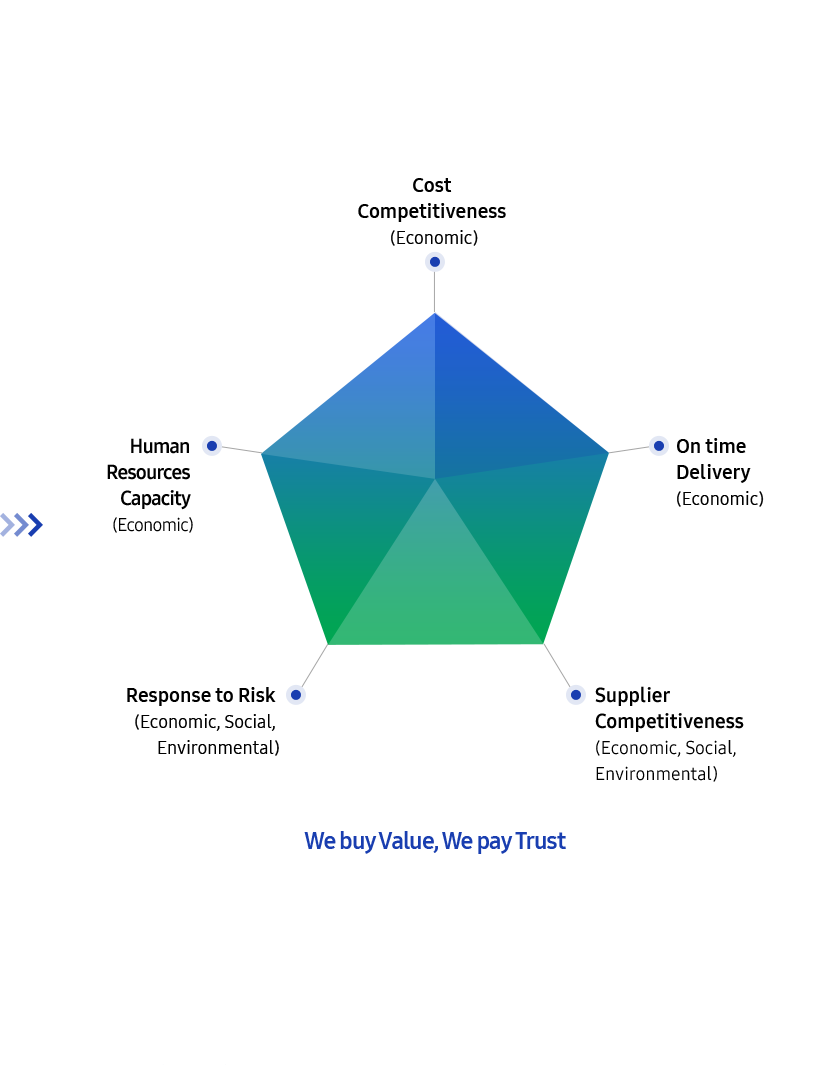
Samsung Value Chain
As Samsung operates globally around the World, it works with aprroximately 2500 suppliers across the globe. Therefore, it is essential for company to build strategic partnerships based on mutual trust and help.Every potential supplier is assessed in accordance to five criterias: Supplier CompetitivenessResponse to RiskOn-time deliveryHuman Resource capacityCost Competitiveness
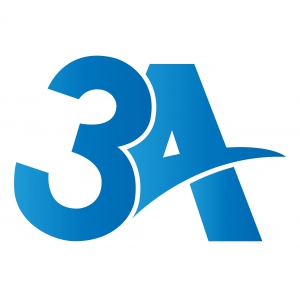
Triple A
During Session 17 we discussed the essential framework of Triple A:AgilityAdaptability Aligment.The case study Amazon Go demonstrated how this framework can be applied in a company and therefore improve company's perfomance.
Agility
Alignment
Its first, second and third-tier suppliers each receive EHS consultation, worksite assessment and product stabilisation to ensure best practices are applied.
Adaptability
Mobile manufacturing plant
Check out the attached video with a short tour of Samsung factory to see how the manufacturing line is working. Company actively uses robots in order to increase productivity and eliminate errors in the manufacturing process.