Lean Management in Naples International AirportMartina ProdomoMIM - Section 2Mind Map - Operations & Supply Chain ManagementProfessor: Felipe Amado Quintana Navarro

Customer Journey Map
During Session 2, we discussed about Customer Journey Map. This tool visually illustrates customers’ processes, needs, and perceptions throughout their interaction and relationship with an organisation.
Departure
I made my own CJM of the departure to let you see the Customer Journey specifically for Naples Airport.
dArrival
I made my own CJM of the arrival to let you see the Customer Journey specifically for Naples Airport.
dAirport CJM
Customer Journey Map is also a Lean Tool part of Value Stream Mapping. In a CJM you identify the pain points and a passenger experience: airports have many pain points as we can see in this article. Understanding very well the pain points we can build the O&SCM and innovation to reduce and reduce those pain points, promote understanding, identify bottlenecks, balance the process and easily train new staff. The picture attached shows how the Airport Ecosystem will change in the next 20 years. The Airport is seen as a small city, it is not only about travelling but it will include every facility we have in cities, such as public transportation, malls, shops ecc.
Customer Experience Frameworks
The Customer Experience was also analysed during Session 12, as the professor presented two important frameworks: 10 lessons of Delivering Excellence Service and 10 Principle of Schmitt.According to these framework, Naples Airport follows the fifth principle of Schmitt:think about the user experience, not about your product service. The airport is a service that is very standardised and it is obliged for customers to use it in order to travel. Many may think that for this reason, they should not concentrate on the customer experience to increase the users. This is not what Naples Airport does, it puts the customer in the center of the service they are releasing.Nevertheless, this Airport has a pain point in the customer experience. Referring to the 10 lessons of Delivering Excellence Service, the lesson that the Airport does not deliver is the sixth lesson, which is to create and sustain a strong service culture. Me, as a frequent customer, I realised that there is not a great culture behind this company but employees just go there because they have to work and are not happy to be there.
10 Principle of Schmitt
10 lessons of Delivering Excellence Service
Introduction
The topic for my mind map is the Naples International Airport, in the specific how Lean Management contributes to che Customer Experience in the airport. I chose this topic because this is the perfect example of how Lean Managements positively affects companies. Thanks to the use of these tools, the airport is in the top 5 list of the most efficient airports in Italy.Additionally, living abroad, I am a frequent customer for airports, in particular this one. When we started studying Lean Management and Customer Experience, I thought about how this could apply to my home town airport.
The company
The Airport
Customers:10 million passengers in 2019. This number is in continuous growth, there has been a growth of 41% from the start of the renewal.The most popular destinations are Milan, London and Venice.55% national destinations vs 45% international destinations.
Lean Management
In Section 7 we discussed about Lean Management and its tools.Lean Management consists in reducing wastes in companies. The following formula perfectly describes what this type of management is:LT = max Value - min WasteLean Management with its tools removes the following downsizes:Defects: efforts caused by rework, scrap, and incorrect information.Overproduction: production that is more than needed or before it is needed.Waiting: wasted time waiting for the next step in the process.Non - Utilised Talent: underutilising people's talents, skills and knowledge.Transportation: unnecessary movements of products and materials.Inventory: excess products and materials not being processed.Motion: unnecessary movements of people.Extra - Processing: more work or higher quality than is required by the customer.Lean Management was born in the Toyota company, but then applied not only in manufacturing companies but also in service.We will see now how these tools are applied to Naples International Airport, in particular to parkings, drop-off and pick up, check - in, and security controls.The most important waste that Naples Airport reduces is waiting time. Waiting time is an important waste to eliminate because it increases costs in a company and generates unsatisfied customers. We talked about the 8 principles of waiting during Session 15:Unoccupied time feels longer than occupiedPre-process wait feel longer than in-processAnxiety makes waits seem longerUncertain waits are longer than known Unfair waits are longer than equitable The more valuable the service, the more waitSolo waiting feels longer than group
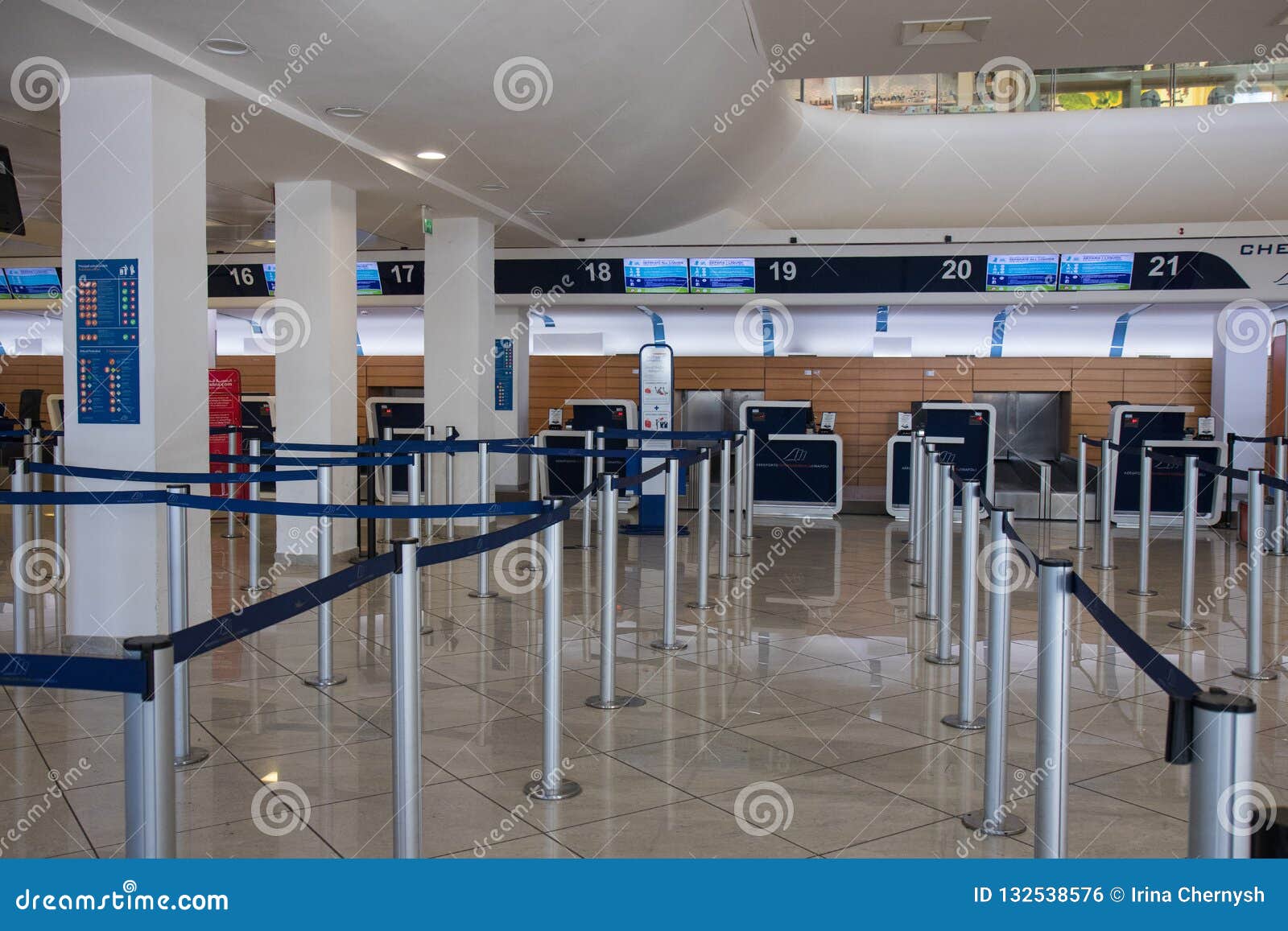
Check - in
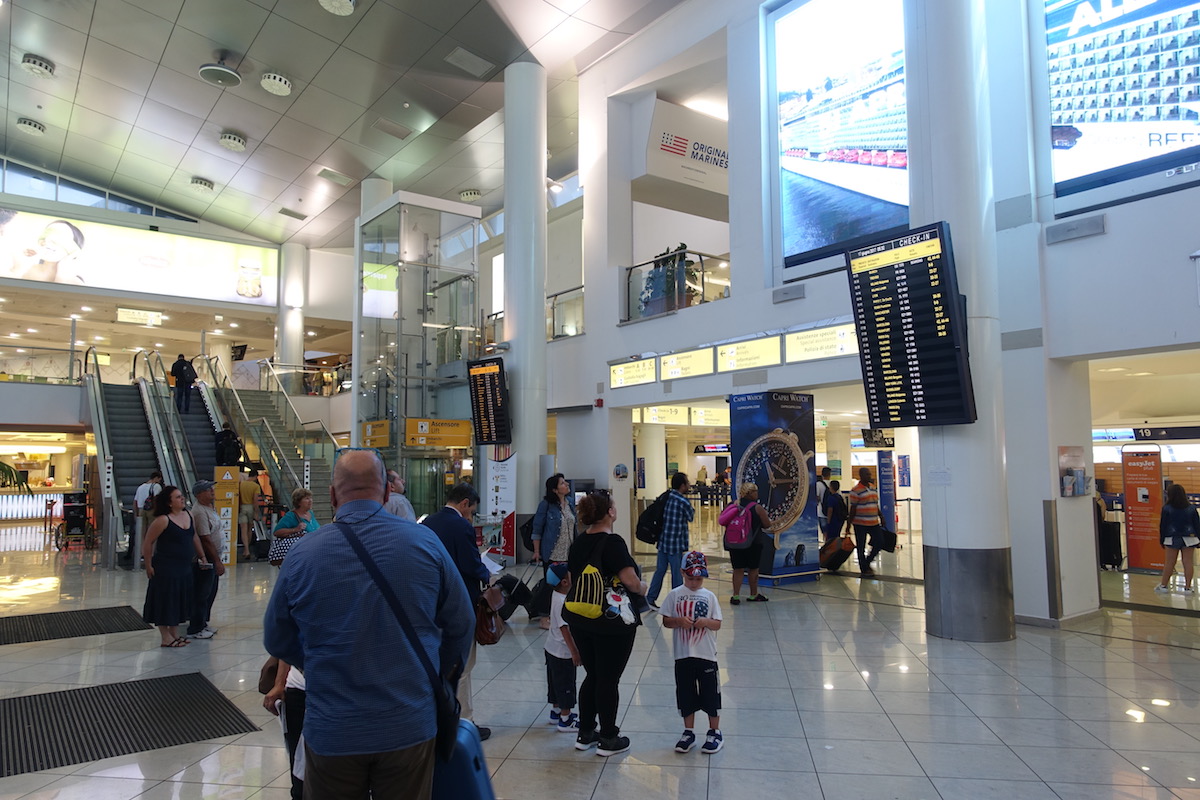
Departure Board
Naples Airport, as every airport, has a departure board as soon as the customer enters the terminal. In this board there is a list of the upcoming flights, with destination, time and number of check-in desk. This is a perfect example of Andon Board, a Lean tool that reduces waiting time and defects.
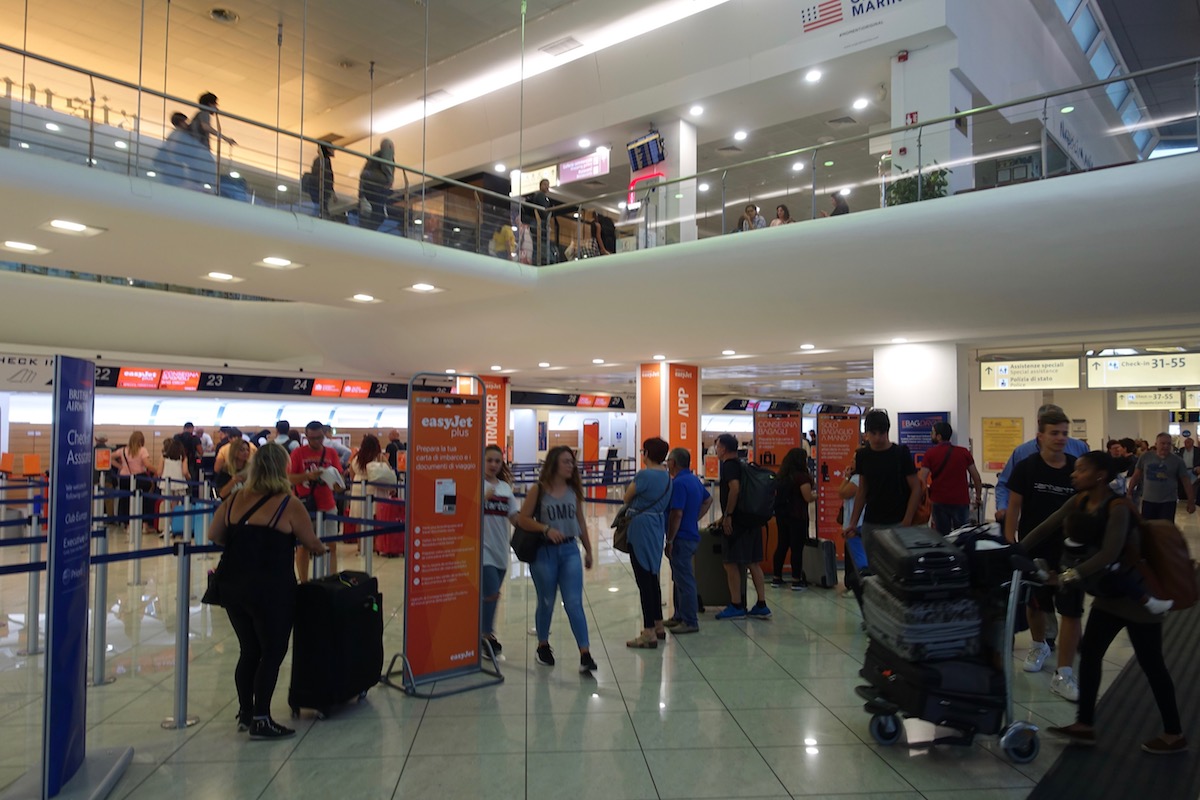
Check - in Desk
Another bottle-neck of the airports is the bag drop-off. in the moment the employee tells the customer that the luggage is too heavy, the queue starts to be longer. The customer has to open the luggage in order to reduce the weight. Naples Airport in order to reduce the waiting time, installed scale before the queue. If the luggage has the correct weight, the machine will automatically print the receipt and the customer is able to start the queue to reach the check-in desk.
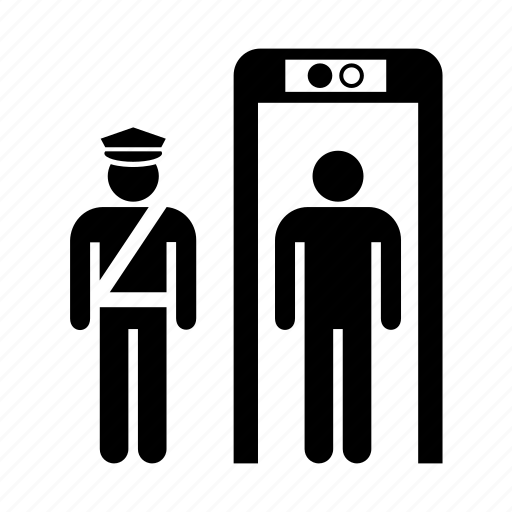
Security Control
Lean Management affected mostly security controls in Naples Airport.Security controls include fast tracks, Automated Pre-Security Gates, queue estimated time and security gate.
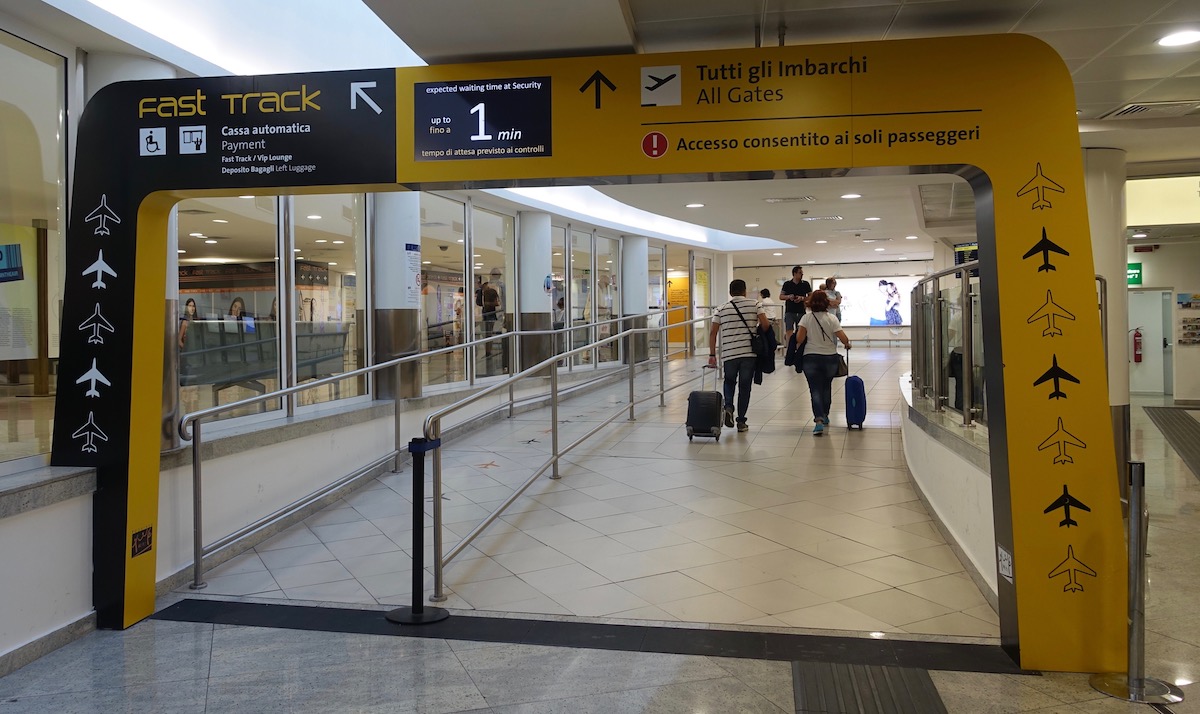
Fast Track
As soon as customers enter the security control zone, they have the possibility to buy the fast track for 5€. This helps passenger that are late or that don't want to spend time in the queue to speed up their customer journey. This tool is reducing waiting time.
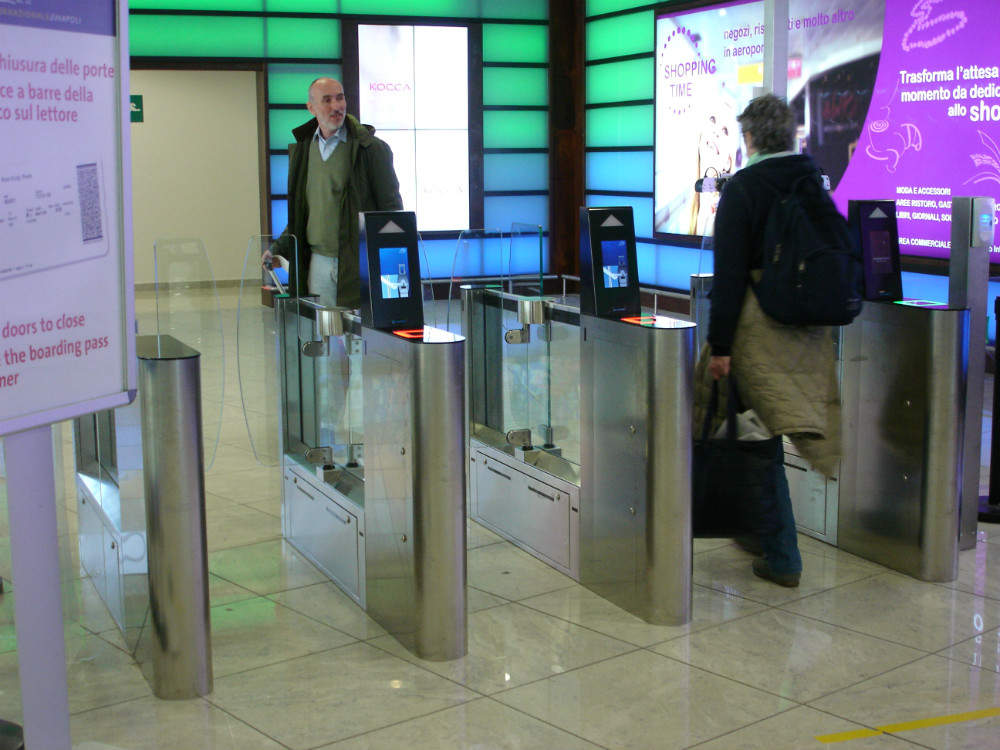
Automated Pre-Security Gates
Introducing the Automated Pre-Security Gates, the airport has used Jidoka. Jidoka, is a Lean tool that automates the process and detects immediately errors during the process. In the specific it reduces waiting time and defects. When entering the security hall, customers have to scan their ticket QR code. This machine detects if the ticket is fine, and in this case opens the gate in order to enter the hall.
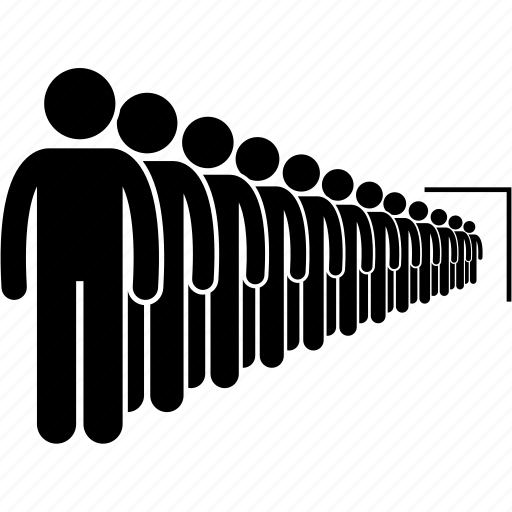
Queue Board
Once the customers enter the hall, there are 5 security gates. At the beginning of each security line, there is a monitor that detects how many people are in the line before you and what is the waiting time for each different queue. The customer is then able to decide according to the fastest queue. Traditionally, there is an employee that moves people from a queue to another to reduce the waiting time. Referring to the Lean tools, this monitor is an Andon board, screens showing status and information on the process. It reduces defects and waiting time.

Security Gate
Almost 5 years ago, they improved the security process which represented a bottle neck in the security gate. They realised that the bottleneck during the process was represented by the unpacking, because (see next picture) they could handle just 2 people while the scanning capacity was for 5 bags. So, a simple but very efficient solution, was to just change the previous table with longer ones, in order to change the process from batches to continuous.After this improvement, the bottleneck is not the unpacking anymore but the scanning. As you can see, the whole process can handle a higher capacity per hour.
Pre
Post
Drop - off / Pick - up
WARNING: in order to watch the video and understand, there is the possibility to put subtitles in English!Naples International Airport invested 700 thousands euros, in order to install cameras that records license plates of cars that enters the airport. They have only 10 minutes to drop or pick up the customer that has to travel. If they exceed this time, they will get a fine. This helps the flow of the traffic, because people will not stop in front of the terminal for too long.
Parking
Parking is the first and last action in the customer journey: first if we talk about departure and last for arrivals.Naples International Airport has 5 parkings, both indoor and outdoor.These reduce wastes for the customers. In the specific, they use Lean Six Sigma reducing waiting time, motion and extra-processing.Every parking has the possibility to enter and pay thanks to a camera that detects the number of the license plate. Customers don't have to wait for the ticket and at the moment of the payment do the queue. All parkings are next to the arrivals and departure terminals, in particular P3 that has direct access to the terminals. There is no need to use a bus to move from the parking to the terminal with a bus (like in many airports around the world).

Sustainability
The topic of Session 16 was Sustainability. Naples International Airport invests in sustainability programs. It uses a website that takes track of the investments, the emissions and news. Naples Airport has been the first of airport to use electric buses.
a